レブロンジェームズ怪我
<ウェブサイト名>
<現在の時刻>
TOP ニュースリリースガイド ニュースリリースガイド一覧 新エネルギー 省エネルギー 材料 Focus NEDO FocusNEDO一覧 Focus NEDO第88号/特集 人とAIが協力し合う未来へ 次のAIが見えてきた Focus NEDO第87号/特集 省エネ・脱炭素への道をひらく 未利用熱エネルギー活用技術 Focus NEDO第86号/特集 AIエッジコンピューティング Focus NEDO第85号/特集 材料開発の革新に三位一体で挑む 超超プロジェクト 第84号/カーボンリサイクル・窒素循環・アンモニア発電・プラスチックリサイクル 資源循環社会への道 第83号/日本の主力エネルギーを目指す 再生可能エネルギー 第82号/イノベーション創出を加速 スタートアップ支援 第81号/実用化へのカウントダウン『セルロースナノファイバー』 第80号/イノベーションで未来をつくる NEDO40年のあゆみ 第79号/ムーンショット型研究開発事業-地球環境の再生へ Cool Earth & Clean Earth 第78号(技術戦略研究センター/スマートセル技術) 第77号(AI・ロボットのNEXTステージ/『オープンイノベーション白書』で読み解くイノベーション創出の今と未来) 実用化ドキュメント 実用化ドキュメント一覧 新エネルギー 省エネルギー 環境問題対策 電子・情報 材料 ロボット・AI・福祉機器 バイオ・医療 NEDO Channel NEDO Channel一覧 新エネルギー 環境問題対策 電子・情報 ロボット・AI・福祉機器 国際 分野横断 その他 NEDO Channel --> 検索 NEDO Channel NEDO公式X NEDO公式Facebook NEDOホームページ トップページ 実用化ドキュメント 構造タンパク質の人工合成で、持続可能性の高い社会に向けた新素材を開発 CONTENTS INTRODUCTION 非石油由来、微生物で新素材を実用化 BEGINNING 人工合成クモ糸の実用化を目指し、学生時代にスタート BREAKTHROUGH 大量生産への道を探る FOR THE FUTURE 目的の繊維を作ることができる「ブリュード・プロテイン™」として再出発 FACE アクセルとブレーキの関係 なるほど基礎知識 NEDOの役割 メニュー閉じる 材料 「イノベーション実用化ベンチャー支援事業/超高機能フィブロインファイバーの実用化開発」他 構造タンパク質の人工合成で、持続可能性の高い社会に向けた新素材を開発 Spiber株式会社 取材:Oct. Nov. 2020 INTRODUCTION 概要 非石油由来、微生物で新素材を実用化 Spiber株式会社(山形県鶴岡市)は、世界に先駆けて構造タンパク質の量産化技術を確立した大学発ベンチャーです。開発する素材は、従来の化学繊維と異なり、石油資源ではなく植物資源を使用して微生物発酵によって作られた構造タンパク質を主原料として使用しているため、持続可能性の高い素材として注目を集めています。そして、構造タンパク質の量産化に向けた研究開発は、2013年にNEDO「イノベーション実用化ベンチャー支援事業」に採択されたことで加速していきました。開発素材の機能性や環境親和性は、スポーツウエアメーカーの株式会社ゴールドウインの目にも留まり、両社は構造タンパク質素材を使用したアウトドアジャケット「MOON PARKA」の研究開発に着手し、2015年にそのプロトタイプを発表しました。そして、2019年に一般販売(数量限定)を成し遂げました。 BIGINNING 開発への道 人工合成クモ糸の実用化を目指し、学生時代にスタート Spiberは2007年に取締役兼代表執行役を務める関山和秀さんと取締役兼執行役の菅原潤一さんが立ち上げた、大学発のバイオベンチャーです。菅原さんは当時を振り返り、「私たちが学んでいた慶應義塾大学環境情報学部には、学生自らが研究プロジェクトを立ち上げることが格好よい、という研究文化があり、研究室の先輩だった関山と、いつか自分たちもと夢を語り合っていました」と言います。 2004年当時、大学4年生の関山さんと2年生の菅原さんは、研究室の合宿に参加しました。菅原さんは、「その合宿の飲み会で、関山たちとたまたま、“クモの糸ってものすごく強くて軽いらしい”という話題で盛り上がって、さらに“NASAでもクモ糸の特性に注目していたが、その人工合成には成功しなかったらしい”という話になりました」と振り返ります。 「関山がそこで、それならもしクモ糸を人工量産できたら、新しいビジネスになるのではと言いだしました。それが、すべての始まりです。合宿から戻って調べてみると、やはりクモ糸は優れた性質を持ちながら誰も人工量産を実用化できていないことを確認できました。そこで、その実用化を目標に『スパイバープロジェクト』を研究室内に立ち上げました」(菅原さん) 天然繊維最強のクモ糸を作り出す微生物と、その特性を示すタンパク質の遺伝子配列を探る 天然繊維の中でも“最強”とも評されるクモ糸は、「フィブロイン」と呼ばれる構造タンパク質からなる繊維で、特に「タフネス」と「高速ひずみ特性」に優れています。「タフネス」とは、強度が高い上に、よく伸びることを意味します。強度と伸度の両立は難しく、それを実現する人工繊維は存在しません。 また「高速ひずみ特性」とは、低速で引っ張った場合と、高速で引っ張った場合とで、強度が変わる特性のことですが、一般的に高強度と言われている繊維でも、高速で引っ張ると強度は下がってしまいます。それに対してクモ糸は速く引っ張るほど強度が上がる傾向を示します。 しかし、クモ糸がどんなに優れていても、生産量を確保できなければ、実用化はおろか実験もできません。そこで関山さんと菅原さんは、クモ糸を大量生産する方法を模索し始めました。カイコのようにクモ自体に糸を生産させることも考えられましたが、生産効率が良くないことから、微生物を利用した発酵で生産する方法に目を付けました(参照:なるほど基礎知識)。 関山さんと菅原さんは、さらにどの微生物にどのようなクモ糸を作らせるかを検討しました。菅原さんは説明します。「当時知られていたクモ糸タンパク質の遺伝子配列は数種類でしたが、その中から目的に合いそうな遺伝子配列を選び、2007年にはクモ糸タンパク質に由来する構造タンパク質を人工生産する目途がつきました。それを機に起業し、社名はクモを意味する“Spider”と、繊維を意味する“Fiber”に由来しています」 効率向上と糸紡ぎに苦心して、やっと完成した一着の青いドレス 微生物が発酵生産した構造タンパク質は、溶媒に溶かして押し出して糸にします(写真1)。この紡糸作業を1回行うのに、少なくともグラム単位の構造タンパク質が必要です。 写真1 紡糸工程(写真提供:Spiber) 生産効率を上げるために、Spiberでは、タンパク質の遺伝子配列を変える「分子設計」技術を取り入れました。また、培地の中で微生物を高密度に培養する方法の検討も行いました。 いくつもの改良により、生産効率は当初の約1万倍にも上がり、起業時にはラボの培養装置から数ミリグラムしか得られなかった構造タンパク質が、グラム単位で得られるようになりました。 ようやく実験に十分な量の構造タンパク質が手に入るようになり、紡糸技術開発が進み始めた頃、Spiberは、世界で初めての、人工合成された構造タンパク質繊維で織られた布による発色も鮮やかな「青いドレス」を縫製し、2013年、六本木ヒルズで発表しました(写真2)。 写真2 人工クモ糸で制作・発表された「青いドレス」(写真提供:Spiber) この「青いドレス」制作に携わった、Biz Dev & Sales セクション・Fiber Developmentチーム兼任の五十嵐瑞季さんは、「生産効率が上がったと言っても、まだラボレベルより少し大きい程度でした。1回の培養で得られるタンパク質はまだ少なかったので、約2mの生地を作るのに、24時間シフトを組んで人力でタンパク質を生産し、必死に糸を紡いだことを覚えています」と当時を振り返ります(写真3)。 クモ糸に着想を得た構造タンパク質素材で作られた光沢のある美しい「青いドレス」は、世の中に大きなインパクトを与えました。Spiberは、アパレル業界をはじめ新素材を求める各方面から一気に注目されることとなりました。 写真3 ラボレベルの培養装置(写真提供:Spiber) 不採択4回でも連続応募、5回目でついに採択 そうした中で、Spiberにターニングポイントをもたらしたのが、小島プレス工業株式会社との業務提携でした。トヨタ自動車株式会社の協力企業として、自動車の内外装部品の製造を行っている同社では、クモ糸由来の構造タンパク質素材の潜在力の高さを見込んで、自動車部品への応用に強い興味を示しました。 菅原さんは、「小島プレス工業からは、構造タンパク質素材の短所、長所を見極めるために、とにかく何か部品を作ってみようという提案がありました。しかし、自動車部品となると、ただ一部品だけでもキログラム単位の素材が必要になります。そのためには生産規模を、ラボレベルから試作規模へと押し上げなくてはなりませんでした」と当時の状況を話します。 当時NEDOは、研究開発型ベンチャー企業の先端技術シーズや有望な未利用技術を活用した実用化開発を支援する「イノベーション実用化ベンチャー支援事業」を設けており、Spiberは、この事業に生産設備のスケールアップ研究を目的として2013年に応募し、採択されました。 創業期からSpiberに関わり、NEDOプロジェクト当時、研究開発実務を菅原さんから引き継いだ森田啓介さん(現:Spiber (Thailand) Ltd.取締役)は、「実は、2013年以前にもNEDOプロジェクトに応募していましたが、4年連続不採択に終わっていました。当時は私たちの技術も未熟で、信用もありませんでしたから仕方がないのですが、小島プレス工業と業務提携したことが功を奏して、やっとNEDOプロジェクトの支援を受けられることになりました」と打ち明けます。 BREAKTHROUGH プロジェクトの突破口 大量生産への道を探る SpiberはNEDO支援の下、試作研究設備である「Prototyping Studio(プロトタイピング・スタジオ)」の建設に着手しました。この設備は構造タンパク質生産に用いる、発酵設備、精製設備、紡糸設備、糸加工設備から構成され、自動車部品の試作を行うことを目的としたものです。業務を進めるにあたり、これまでとは比較にならない規模の発酵設備の設計とオペレーションを任されたのが、現在、品質保証セクションのマネージャーを務める鈴村寛昭さんでした。 鈴村さんは、「創業者二人の研究室の後輩として、学生の頃から遺伝子を作ったり、発酵生産したり、それを精製したりと研究に関わっていました。その経験を買われて、『Prototyping Studio』に導入する発酵タンクを設計することになりました」と話します。 「しかし、もともと実験室で小さな設備は扱っていましたが、そのような大スケールのタンクでの生産や発酵経験はもちろんありませんでした。設備メーカーや開発協力先の発酵メーカーの間を何度も行き来して助言をいただきながら検討を重ねましたが、構造タンパク質生産に最適な設備を設計するのには、かなり苦労しました」(鈴村さん) また、設備ができてからも、「研究室と同じことをしているつもりでも、容量が大きいと、例えば均一温度になる時間が変わったり、原料を輸送する配管が太くなり、圧力が変わって発酵に影響したり…、とにかくトライアル&エラーを繰り返しました」と鈴村さんは言います(写真4)。 写真4 「Prototyping Studio」内に整備された発酵設備(写真提供:Spiber) こうしてタンパク質を発酵により微生物に生産させ、タンパク質だけを取り出すために精製し、糸に加工するという一連の流れを行う「Prototyping Studio」が完成、1,000倍まで生産規模をスケールアップさせることができました(写真5)。ここには、これまでSpiberのメンバーがラボレベルで培ってきたノウハウの全てが、注ぎ込まれました。 写真5 「Prototyping Studio」建屋全景(写真提供:Spiber) 天然ガス用高圧タンクへの実用を模索 さらに翌年の2014年には、引き続き、Prototyping Studioで試作した構造タンパク質の天然ガス用高圧タンクへの適用を研究開発するNEDOプロジェクトに参画しました。 天然ガス用高圧タンクには、内圧に耐えられる強度が求められます。炭素繊維をアルミやプラスチックでできたライナーに巻くことで強度を上げることができますが、そこに構造タンパク質も使ってみようという試みでした(写真6)。 写真6 NEDOプロジェクトで試作した天然ガス用高圧タンクの製造ライナーの強化(写真提供:Spiber) 菅原さんは、「炭素繊維だけではタンクが破裂してしまうような条件でも、構造タンパク質を巻くことで、破裂に到らず変形のみになったという結果が得られました。構造タンパク質の特性が活かされたのです」と話します。 「ただ、加工過程や性能面で課題は残りました。プロジェクト後もタフネスを付与できるという特長を活かした自動車部品を、小島プレス工業と共同で開発を続けています」(菅原さん) この年度のプロジェクトでは、Prototyping Studioを導入し構造タンパク質を量産したことにより顕在化した課題を解決するために、培養や精製の設備改良や増強も行われました。 脱石油資源を視野に、アパレル業界に参入 高圧タンクへの適用研究が続く一方で、「Prototyping Studio」で試作したサンプル(写真7)は、さまざまな企業の手に渡り、注目を集めました。その背景にはNEDOプロジェクトに採択されたことで、信用度が増したことがあったと菅原さんらは指摘します。以降、Spiberは、数多くのパートナー企業や金融機関から多くの資金を調達することができました。また、そこから新たな事業展開の芽も出てきました。その一つがアパレル事業です。 菅原さんは、「ゴールドウインの現在の社長と2014年にお会いして興味を持っていただき、同社が日本で展開するアウトドア用品ブランド『The North Face』で、アウトドアジャケットを共同開発することに決まりました。それが『MOON PARKA』です」と話します。 厳しい自然環境の中で着用するアウトドアジャケットには、高い機能性が求められるため、新素材の開発や利用は難しいとされてきました。一方で、高い関心が寄せられたのは、Spiberが開発する素材が、石油に頼らず植物資源を使用し微生物発酵によってつくられた構造タンパク質を主原料として使用しているため、持続可能性が高く地球環境に優しいということでした。 写真7 Prototyping Studio が稼働した2013年当時に制作された構造タンパク質素材のサンプル(写真提供:Spiber) 菅原さんは、「アパレル市場は巨大で、石油由来の化学繊維を大量生産・大量消費しています。私たちの構造タンパク質素材をアパレル産業の中で普及させることができたら、環境負荷低減に貢献できるのではと、期待に胸を膨らませました」と話します。 プロトタイプ製品発表も、しかし耐水性の問題が顕在化 こうして、Spiberとゴールドウインの両者による共同研究開発プロジェクトが始動しました。Spiberが蓄積した膨大な遺伝子ライブラリから、「MOON PARKA」にふさわしい表地や刺繍糸用のタンパク質を選定し、さらに紡糸、撚糸、織り、縫製など、アウトドアジャケットの製造工程に最適な条件を検討する試作が繰り返されました。 そして、実際のアパレル工業ラインで製造された、世界初の人工構造タンパク質素材による衣服として、「MOON PARKA」のプロトタイプが、2015年に華々しく発表されました(写真8)。 ところがその後すぐ「MOON PARKA」は大きな壁にぶつかってしまいます。五十嵐さんは、「問題になったのは耐水性です。濡れると縮んで型崩れを起こしてしまったのです」と説明します。 「タンパク質はアミノ酸からできているので、水の影響を受けることは予想していましたが、ジャケットでは糸をそのまま使うのではなく、生地にして裏材を貼ったり、撥水コートをしたりするので、その過程で、この問題は解決できると思っていました。ところが、そうした後工程の対応では問題解決に至ることができませんでした」(五十嵐さん) そこでSpiberは思い切った決断を実行します。タンパク質の遺伝子配列にまで立ち返り、もう一度、そこから検討し直すという、なんとも手間のかかる研究開発に取り組むことにしました。 森田さんは、「天然のクモ糸で、水による収縮の原因となるタンパク質の配列を解析して、どうすれば自分たちのタンパク質の問題を解決できそうかを考え、遺伝子配列を操作することでタンパク質を変えていきました」と言います。 写真8 (上)初代「MOON PARKA」に使用された構造タンパク質の撚り糸 (中)同じく織り布 (下) 2015年10月に発表された「MOON PARKA」の初代プロトタイプ(写真提供:Spiber) 「それは、まさにタンパク質そのものを“デザイン”する、という感覚でした。仮説を立てコンピュータでシミュレーションし、より効率的に“デザイン”作業を行ったつもりですが、それでも新たな『MOON PARKA』を発表できるまでに、約4年もかかってしまいました」(森田さん) 一方、鈴村さんは、「それでも4年で済んだのは、新たに“デザイン”したタンパク質をすぐに量産試作し、検討できる『Prototyping Studio』が、NEDOプロジェクトで導入できていたからこそです」と話します。 「NEDOプロジェクトの支援は、プロジェクト中だけでなく、その後も、そして今も、Spiberの研究開発に役立っています」(鈴村さん) こうして実現した新たなタンパク質糸を使用した新生「MOON PARKA」は、ゴールドウインの厳しい品質テストにも合格して、2019年12月に数量限定ながら一般販売されました(写真9)。 写真9 2019年12月に数量限定販売ながらついに市販された「MOON PARKA」(写真提供:Spiber) これまでの道のりを振り返って鈴村さんは言います。「NEDOプロジェクトに採択され試作研究設備『Prototyping Studio』ができるまでは、いろいろな提携や共同開発の話があっても、それに見合う生産量を確保することができませんでした。それが『Prototyping Studio』が動き出してからは、開発のスピードが飛躍的に高まりました。高圧タンクにしても『MOON PARKA』にしても、大量の材料があったから試行錯誤ができました。『Prototyping Studio』は、まさに私たちの事業にとって命綱とでも言うべき存在です」 また、森田さんは、「NEDOプロジェクトでパイロットスケールの設備を持てたことは、実績の少ない私たちには対外的な信用を得る上でも大きな効果がありました」と話します。「鶴岡市の弊社まで多くの、しかもさまざま方がいらっしゃっていただきますが、ラボ設備だけだとまだまだ小規模の開発だと感じられることもありました。しかし『Prototyping Studio』を紹介すると印象が変わって、ビジネスにつながる可能性が飛躍的に高まりました」 FOR THE FUTURE 開発のいま、そして未来 目的の繊維を作ることができる「ブリュード・プロテイン™」として再出発 森田さんは説明します。「新生『MOON PARKA』に最終的に使用された構造タンパク質は、クモ糸タンパク質を参考にはしていますが、生産性を上げるために遺伝子を変え、耐水性の問題を解決するためにまた変え、ほかにも各生産プロセスに、よりふさわしいものにするために改良を加えているので、正確にはもうクモ糸とは呼べないものになっています」 しかし、その4年間に及んだタンパク質との格闘は、タンパク質の遺伝子配列とその物性を相関させる膨大なデータベースとなりました。その結果、Spiberの事業は、クモ糸由来のタンパク質で糸や布の原材料を製造・提供するだけでなく、微生物の発酵・培養で、ユーザーが望む特長を持つ繊維を“デザイン”し、提供できる事業へと成長・変貌を遂げました。 当初はクモ糸の特性の再現を目的とした研究開発を行い、商品名を「QMONOS®」としていましたが、ここから、その上位概念となる「発酵タンパク質」に由来する「ブリュード・プロテイン™」へと変わりました。作りたい製品に合わせて繊維を開発する、すなわち、製品に必要な機能性を優先できるというコンセプトが実現できるようになりました(写真10)。 写真10 「ブリュード・プロテイン™」と各種加工工程で得られた素材の例 A.粉末 B.綿(わた)「ブリュード・プロテイン™」の長繊維を短くカットすることで得られた短繊維を、異なる種類の短繊維と絡み合わせて綿状にしたもの。 C.紡績糸 綿を紡ぐことで得られた紡績糸。主にアパレル用途での利用が期待されている。 D.長繊維(フィラメント糸)「ブリュード・プロテイン™」の粉末を特殊な溶媒に溶かし、別の溶媒中へ吐出することで得られた繊維。アパレル用途や繊維強化プラスチックなど、産業用素材として期待されている。 E.レジン 「ブリュード・プロテイン™」の粉末を加熱圧縮することで得られる樹脂。熱で溶融しない。 F.ゲル タンパク質の種類によって保持できる水分量やゲルの硬さ等を変えることができる。医療・化粧品用途での展開が期待される。 G.スポンジ 「ブリュード・プロテイン™」のゲルを乾燥することによって得られる多孔質体。 H.フィルム タンパク質の種類によって、吸水率や紫外線吸収率などをコントロールすることができる。医療用途や農業資材としての活用が期待される。(写真提供:Spiber) 「ブリュード・プロテイン™」は、すでにゴールドウインだけでなく他のアパレルメーカーにも採用されています(写真11)。そしてゴールドウインでは、スケートボードへの使用など、アパレルを越えた応用にも着手しています(写真12)。Spiberではそうした多様な要求に応えられる特性を有する「ブリュード・プロテイン™」を提案、供給しています。 写真11 2020年のパリファッションウイークでの、「ブリュード・プロテイン™」素材で制作した「YUIMA NAKAZATO」コレクション(写真提供:YUIMA NAKAZATO) 写真12 ゴールドウインが、米国スケートボードメーカーと共同開発中のロングタイプのスケートボード。「ブリュード・プロテイン™」と竹の複合材を使用している(写真提供:Spiber) そして、Spiberは「ブリュード・プロテイン™」の需要拡大に備え、タイに生産工場を建設中で、2021年の稼働を予定しています。稼働後は年間最大数百トンの生産能力を誇る、世界最大規模の構造タンパク質発酵生産プラントとなる見込みです。 さらに米国の穀物プロセッサー大手Archer Daniels Midland Company(ADM)と提携して、「ブリュード・プロテイン™」の米国内での生産を進めることも決まっています。 分子設計、発酵培養によるものづくりが評価されNEDO「スマートセルプロジェクト」に参画 SpiberはNEDOプロジェクト「植物などの生物を用いた高機能品生産技術の開発(スマートセルプロジェクト)」(2016〜2020年度)にも、全期間ではありませんが参画しています。本プロジェクトは、生物機能を活用して新たな産業「スマートセルインダストリー」を起こそうというもので、物質生産能力の高いスマートセルの創出を目指しています。 Spiberの、微生物を用いたタンパク質の発酵生産の豊富な経験と技術が評価され、同プロジェクトに採択されました。このプロジェクトには、ほかにも多くの大学や企業が参画し、協働しています。この中で、微生物の細胞から有用物質を合成するために必要なDNA配列を、ゲノム編集技術等を活用して、高速で合成し評価することを目指した「高生産性微生物創製に資する情報解析システムの開発」を担当しました。 このプロジェクトを通して、今後、どのような素材や材料を生み出していくのか、Spiberが持つ技術と経験の可能性に新たな期待が膨らみます。 開発者の横顔 アクセルとブレーキの関係 代表執行役の関山さんとともに、大学研究室内に「スパイバープロジェクト」を立ち上げ、その後Spiberを共に創業した菅原さんは、代表との関係を「関山はアクセルで、私はブレーキになることを期待されることがあります」と表現します。 「2007年当時、起業意欲は間違いなく関山の方が大きかったですね。私はどちらかというとリスクを見て『技術が未熟、時期尚早』と意見したりしていました。ただベンチャーでは、飛行機が離陸するときのように、とにかくアクセルを踏み切らないとダメな時もあり、そのバランス感覚が重要だと思っています」 「関山との関係は創業当時と変わらず強固です。徐々に加わった仲間の数も多くなって、そうしたメンバーに支えられていると感じることも増えてきました。NEDOプロジェクトへの参加によって、会社も私たちもずいぶん成長したものだと感じています」 Spiber株式会社 取締役兼執行役 菅原 潤一 さん 初めてのスケールアップ経験 関山さんの5年、菅原さんの3年後輩である森田啓介さんは、創業期からのメンバーのひとりです。創業者からの信頼も厚く、2013年と2014年の両NEDOプロジェクトを主導しました。 「以前はラボスケールが中心でしたが、NEDOプロジェクトでは実機を使用した、スケールアップが大きなテーマとなりました。開発メンバーはラボスケールしか経験したことがない者が多かったため、限られた開発期間で行うことは大きな挑戦でした」 「NEDOプロジェクトで得たスケールアップの経験が、現在につながる大きな財産となったと思っています」 Spiber (Thailand) Ltd. 取締役 森田 啓介 さん アパレル事業を切り開く 2009年に入社した五十嵐さんは、テキスタイルチーム等のマネージャーを歴任し、アパレルへの応用に向けた「QMONOS®」素材化を一手に引き受けました。 「最初は1ミリリットルのチューブからタンパク質の原料をピンセットで引っ張って、1日目は〇センチ、2日目には〇〇センチと、どのくらいの長さのタンパク質が取れるか地道に実験していました。それが、NEDOプロジェクトで導入できた『Prototyping Studio』での成果により、今では、目的用途の性質をもつ『ブリュード・プロテイン™』を大規模生産できる設備を備えるまでになりました」 Spiber株式会社 Biz Dev & Sales セクションFiber Developmentチーム兼任 五十嵐 瑞季 さん 発酵設備の設計・オペレーションに挑む 鈴村さんは、冨田研究室の学生の頃からSpiberに関わってきました。2013年の「Prototyping Studio」立ち上げでは、発酵設備の設計という大きな仕事を任されました。 「大きな発酵槽のある生産設備を見学したことはありましたが、それを自分で設計することになるなんて……、勝手がわからない上に、そこに誰も経験したことのない構造タンパク質の発酵プロセスを載せなくてはならないので、苦労しました」 「また、事業規模が大きくなったことで関係する法律や規制が変わり、その対応のために、2~3人で手分けして大急ぎで資格を取得したりしました。想像はしていましたが、研究と実際の生産や事業には、それ以上の大きな違いや発見があるのだと、NEDOプロジェクトを通して実感しました」 Spiber株式会社 Quality Management部門 品質保証セクション セクションマネージャー 鈴村 寛昭 さん なるほど基礎知識 目的用途のタンパク質を微生物に作らせ、糸にする タンパク質を発酵生産するには、まず、①どのような性質のタンパク質を作りたいか決め、それを作るための遺伝子を設計します。②目的タンパク質を作るのに適した微生物に遺伝子を導入し、③遺伝子が導入された微生物の中から、より生産性の高い微生物を選び出します。④遺伝子を導入した微生物を培養して、タンパク質を作らせ、⑤そこから微生物や培地を除く精製を行って、純度の高いタンパク質を得ます。⑥得られたタンパク質を溶媒に溶かし、シリンジに入れ押し出して糸状に加工します(図1)。 この一連のタンパク質の発酵生産、精製、紡糸のプロセスを行うことができるのが、2013年のNEDOプロジェクトで山形県鶴岡市に建設された「Prototyping Studio」です(現在は紡糸設備のみを本社研究棟内に移築、増設)。 図1 目的用途のタンパク質の生産方法(写真提供:Spiber) さらにSpiberでは、⑦作った糸の特性を調べ、遺伝子配列との相関をデータ化しています。このデータに基づいて、目的の性質をもつと予想されるタンパク質の遺伝子をデザインして(分子設計という)、それを微生物に作らせるというサイクルを繰り返しています(図1)。その結果、データがどんどん蓄積し、実際に、目的の性質をもつタンパク質を作れるまでになりました。こうして発酵生産されたタンパク質が「ブリュード・プロテイン™」です。 NEDOの役割 「イノベーション実用化ベンチャー支援事業/超高機能フィブロインファイバーの実用化開発」 (2013年度) (NEDO内担当部署:イノベーション推進部) NEDOは、優れた先端技術シーズを有する日本のベンチャー企業等に対し、当該シーズを基にした実用化開発を支援するための助成事業を実施しています。 世界で初めて、人工クモ糸のような構造タンパク質の合成に成功したSpiberは、本事業により、量産化に向けた研究開発設備を導入し、試作期間がラボレベル規模の頃から飛躍的に加速しました。この人工構造タンパク質は、微生物を利用して生産するので、石油由来品と異なり環境に優しく、また、各種特性に優れています。ゴールドウインが興味を持ち、アウトドアジャケットの共同開発に取り組むことになり、一般販売まで実現しました。 本事業での設備導入により、サンプルの種々の業種への供給や、課題解決期間の短縮が可能となったことで、研究開発成果が事業化・実用化に結びつき、さらに、他分野への適用が進められています。 関連プロジェクト イノベーション実用化ベンチャー支援事業/超高機能フィブロインファイバーの実用化開発(2013年度) 平成25年度 イノベーション実用化ベンチャー支援事業(2014年度) 植物等の生物を用いた高機能品生産技術の開発(スマートセルプロジェクト)(2016年度~2020年度) お読みいただきありがとうございました。ぜひともアンケートにお答えいただき、お読みいただいた感想をお聞かせください。いただいた感想は、今後の連載の参考とさせていただきます。 アンケートに回答する (法人番号 2020005008480) NEDO WebMagazineとは サイト利用について ©New Energy and Industrial Technology Development Organization. All rights reserved. Top -->
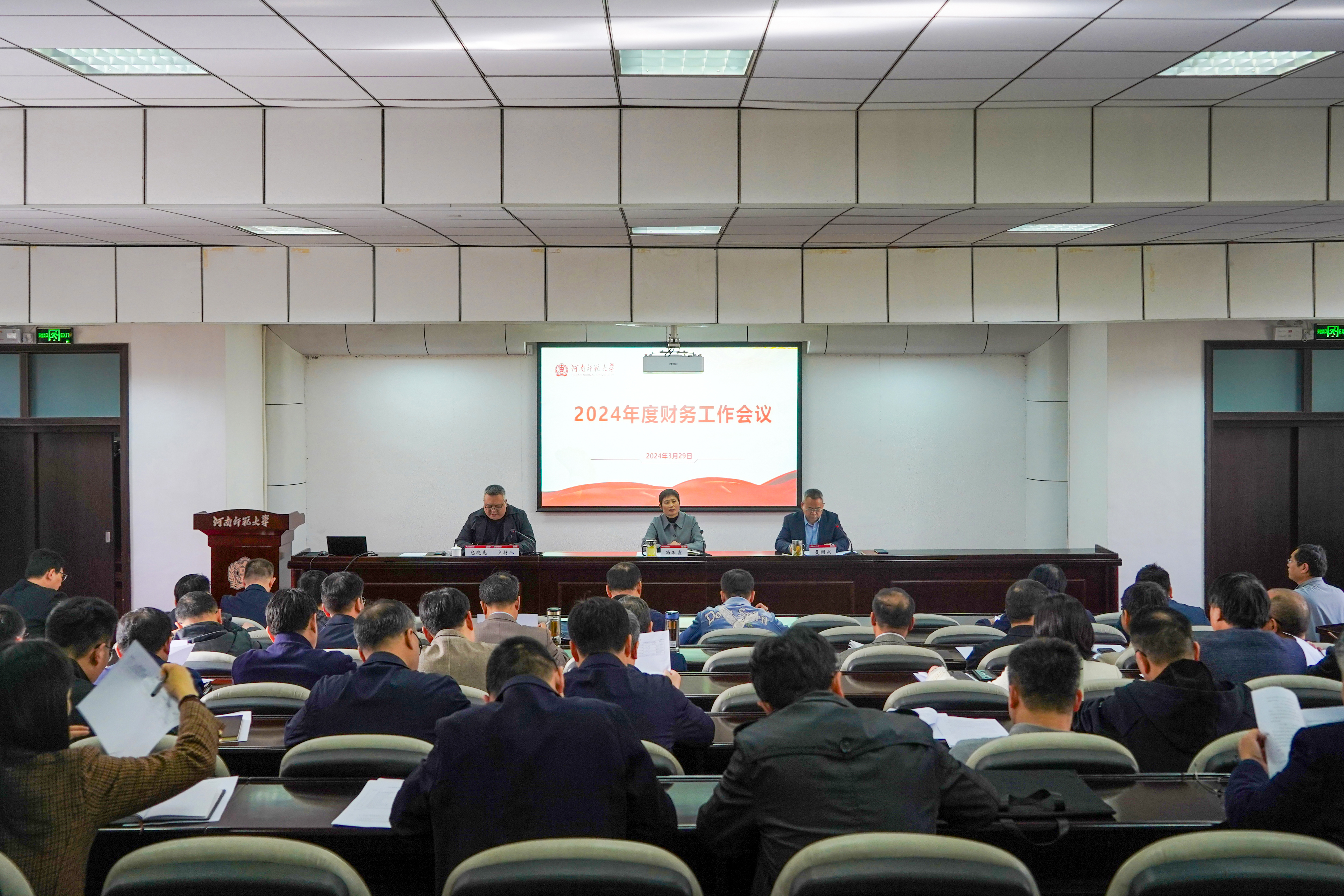