オンラインカジノMGテックライブ - Online Casino MG Tech ...
<ウェブサイト名>
<現在の時刻>
Jumplinks Jump to content Jump to main navigation Jump to sub navigation Jump to service navigation show menu EN English This page is not available in English. EN English Diese Seite ist auf Deutsch nicht verfügbar. DE Deutsch Esta página no está disponible en español. ES Español 此页面不支持中文。 中文 中文 Esta página não está disponível em português. PT Portugues 日本語ページはございません。 日本 日本 ASK Chemicals Search Main navigation Foundry Cold Box Binder Systems Product Finder Cold Box PU Technology Our Brands ECOCURE BLUE LFSPAC No-Bake Binder Systems Product Finder No-Bake Technology Our Brands INOTEC - Inorganic binder system Product Finder INOTEC Technology INOTEC - technological advantages INOTEC - economic advantages INOTEC - ecological advantages INOBAKE - Inorganic No-Bake Binder Product Finder INOBAKE Technology Coatings Product Finder Coating Technology Our Brands Additives Product Finder Additive Technology Uncoated Castings Lithium free Additives Risers & Sleeves Product Finder Experience Expert Feeding Solution EXACTCAST mini-risers EXACTCAST Riser Sleeves & Auxiliary Products Formulations EXACTCAST riser data for simulation Filters Product Finder EXACTPORE 3D Filters UDICELL Filters EXACTFLO Filters UDICELL Investment Casting Filters Auxiliaries & Release Agents Release Agents Adhesives Cleaners Other Auxiliaries Metallurgy Products Product Finder New Generation of Mold Inoculants Master alloys Cored wire Inoculants Mold Inoculants Pre-conditioners Melt cleaners Design Services Arena-flow® Software From Concept to Design Simulation Services Core Production Expertise & Quality Our Offer Services Success stories Industrial Friction Selector Guide Wear Resistant Friction Resins Refractory Product Advisor Technical Bulletins Success stories Paints & Coatings Product Finder Paints & Coatings Architectural Coatings Can Coatings Wood Coatings Industrial Coatings Protective Coatings Conductive Coatings Additives Fertilizer Coatings General Industrial Latex, textile and special paper applications Carbon Products Resins For Jointing Compounds Toll Manufacturing Innovation Highlights 3D Binder Systems Environment Efficiency & Performance Optimizing costs in use Controlled release fertilizer coating Support Online Academy Live Webinars On Demand Webinars ASK the Expert Ask your question All Questions Casting defect prevention Product usage Environment Profitability Digital Services ASKNow Mobile Download Windows Download ASK Vista Tutorials & Videos White Paper Reduction of VOC emissions New Emission Limits User Manual Professional Articles MAGNASET 2.0 Fluorine-free Riser Filter - Process improvement Release Agents - Correct Classification Filter - Reducing costs in large castings Coatings Saving Potential Sand Binder Systems More Technical Paper Brochures Quality Management Sales Terms & Conditions of Purchase Company History Sustainability Diversity Compliance Quality and environmental certificates News Press releases Shows & Events Career Our Vacancies Your New Employer ASK & ME Our Expert&#039;s Voice Your Start Your Application Contacts Get in touch with us Foundry Chemicals Locations Paint & Coating Industrial www.ask-chemicals.com Support ASK the Expert Environment Environment reset filter Does the global role-out of inorganic binder technologies determine the end for conventional shell sand processes? Inorganic binder technologies gain an increasing attention, not only in the European foundry industry. Does the global role-out of inorganic binder technologies determine the end for conventional shell sand processes? Our US experts recommend: A provocative question, I must admit, and the answer to this question is diversified in respect to the casting application. Of course, new technologies always threaten the existence of conventional technologies as far as they add performance value to the respective process itself. In case of aluminum casting applications, particularly in high productive segments such as the manufacture of aluminum engine blocks and cylinder heads in permanent mold casting, more and more foundries are converting from organic to inorganic binder systems – and there are several reasons for this trend. Odorless core production, no harmful emissions during casting, less maintenance of machinery and tools, and the resulting higher productivity are well known economic and ecological benefits of the INOTECTM technology. Technological benefits rely on the faster solidification of the aluminum melt. Reduced die mold temperatures and the consumption of energy from the aluminum melt by water evaporation result in improved mechanic properties of the castings, e.g. reduced dendritic arm spacing. The inorganic binder technology INOTECTM is described as a two component binder system including a liquid INOTECTM binder and a solid inorganic additive – the so-called INOTECTM Promotor. Shell sand is a phenolic resin coated sand with addition rates of 2,5 to 3,5% (based on sand). In terms of core manufacturing, both binder systems are cured in a hot core box. INOTECTM requires significantly lower core box temperatures (150 – 210 °C vs. 250 °C for shell sand) but also implies the necessity of hot-air purging that is missing in the shell sand process. Strength values (both hot and cold) of INOTECTM-bound cores are high enough for automatized handling. Care should be taken in regard of the brittleness which is typically higher than that of shell sand cores. Additionally, inorganic-bound cores have – by nature – a high affinity to water. Thus substantial technical adjustments (storage facilities with proper storing conditions to avoid exposure to high humidity) and continuous product development to improve humidity resistance are countermeasures. A major disadvantage of shell sand cores are volatile emissions during core manufacturing as well as odor and smoke formation in the casting production process as a results of the thermal decomposition of the phenolic resin. As a consequence, condensate or tar build up reduce die mold lifetimes and imply continuous maintenance operations. Additionally measures, e.g. ventilation and air treatment systems, are mandatory. Higher risks for gas inclusions and casting defects are possible as shown by the difference in gas formation potential. The amount of condensate for INOTECTM is related to the amount of released water that contribute to the binding properties of the silicate gel structure during core manufacturing, storage and utilization. Binder system INOTECTM Shell sand Gas volume [ml] 40 324 Condensate [mg] 139 397 Comparison of gas and condensate formation between shell sand and INOTECTM. Measurement was done using a COGAS apparatus in liquid aluminum. Dimensional casting accuracy as a result of improved thermal stability is comparable for both binder systems. The INOTECTM tooling kit approach even enables tailor-made core property adjustments in respect to thermal strain and core geometry. Core collapse or shake-out processes for inorganic-bound cores require mechanic impact via hammering and vibrating systems. Continuous product development and process discipline enable reliable core collapse properties even of complex cores on serial production scale procedures. In comparison to shell sand cores, the INOTECTM technology shows equal or even superior process properties during core manufacturing and aluminum casting production, if technical measures, process knowledge and process discipline are established. So, consult with your ASK Chemicals contact for the best overall recommendation. What does "Sustainability" mean for foundries? Q :The topic of sustainability ” has been on everyone’s mind for some time now. What exactly does this mean - for my foundry? A: The definition of sustainability rests on three pillars – ecology, economy and society. The last two of these often are neglected when projects are being developed and assessed. Sustainable products, however, are able to contribute much more to achieving sustainability than people may initially think. Anyone who has ever been to a foundry that has been converted from organic to inorganic binder technology, and has seen how that technology and work environment has changed to the benefit of the workforce, will recognize the economic and social contribution it provides. When it comes to economic sustainability, the question for foundries is how to increase economic success while at the same time maintaining the quality and availability of resources. This is where metalcasting industry suppliers are able to make a contribution by developing solutions that replace potentially harmful, scarce, or expensive raw materials with others that deliver equal or enhanced performance. A good example is ASK’s ECOCURE BLUE binder technology for iron casting. It uses the world’s first phenolic resin for the cold-box process that does not require statutory labelling in the market, in accordance with the CLP Regulation for the classification, labelling and packaging of substances and mixtures. Therefore, the ECOCURE BLUE binder is no longer considered a hazardous material. The utilization of this innovative cold-box binder technology can result in significantly reduced phenol and formaldehyde emissions. Foundries want to reduce the emissions resulting from their processes. Emissions have negative and potentially irreversible consequences for the environment, and so foundries are incentivized to adopt new technologies, not only to continuously meet regulatory and environmental requirements but also to satisfy the increasing expectation of social responsibility. Therefore, ASK Chemicals has been researching and developing new products for many years to achieve reductions in emissions caused by their products. The preservation of resources – rare, readily available, or seemingly ubiquitous and plentiful – is surely another important topic we have to consider. An example of such a resource is lithium, which is extracted from the ground at a grave environmental cost, particularly in South America, where the mineral reserves are being exploited to supply the dramatic increase in demand for lithium to support electric fuel-cell production. ASK Chemicals has been a driving force behind the development of lithium-free sand additive product solutions for quite some time now. Q:The demands on foundries to reduce CO2 emissions, in order to achieve CO2 neutrality, are becoming increasingly stringent. What is ASK’s assessment of this situation? A:The obvious approach to achieve CO2 neutrality is to manufacture products from renewable raw materials. But that is just one aspect of product development and cannot be the only driving force. To achieve CO2 neutrality, designers and manufacturers must take into account a product’s entire lifecycle, and consequently all the processes used to produce the raw materials involved in production are just as important as the manufacturing processes that result in end products with the desired (i.e., CO2 neutral) performance profiles. This is why ASK Chemicals has a clear focus on enhancing its products’ efficacy, in getting things done, while minimizing the burden on the environment from cradle to grave. Treating Sand to Improve Air Quality and Casting Results The right sand additive can address EPA’s HAP standards and reduce atmospheric dust and smoke in the workplace – while enhancing the quality of finished castings. How can we reduce smoke and emissions in our foundry and at the same time produce defect-free castings? The Environmental Protection Agency sets emission standards for hazardous air pollutants (HAPs) at foundries – many of which are traced to the emissions that result from chemical binders used in mold and core making. Some organic HAP emissions include benzene, toluene, and xylene (BTX) as well as naphthalene. VEINO ULTRA™ NB-LOSMK is a sand additive developed by ASK Chemicals to reduce these emissions by as much as 30% in no-bake molding applications. In addition to reducing emissions, VEINO ULTRA™ NB-LOSMK also reduces smoke, which contributes to an improved working environment for foundry personnel. By removing the smoke from the air, workers’ line of sight is improved substantially. When working with most sand additives, it’s necessary to increase the amount of the binder being used in order to compensate for a decrease in tensile strength that results due to the addition of high-surface area, finer particles. VEINO ULTRA™ NB-LOSMK’s size distribution has been optimized in order to minimize the negative effects on tensile strength. The speed of the reaction, including the work time and strip time, may be adjusted with slower or faster catalysts, depending upon the needs of a particular foundry. As with standard sand additives, VEINO ULTRA™ NB-LOSMK will combat veining, penetration, and surface finish defects in addition to lowering emissions and smoke. Furthermore, it has the ability to scavenge for various mold gases For those foundries that reclaim sand, either mechanically or thermally, sand additive build up in the reclamation system may be a concern as tensile levels for the sand will diminish over time. These worries are negated by VEINO ULTRA™ NB-LOSMK, as the particles will be drawn off in the foundry’s dust-collection system. VEINO ULTRA™ NB-LOSMK provides a solution to smoke and emissions in the foundry, and will working conditions for operators. FoundryIndustrialPaints & CoatingsInnovationSupport CompanyCareerContacts Follow us on: Service navigation Sales Terms & Conditions ASK News Data Protection Disclaimer Imprint & Trademarks © ASK Chemicals 2024
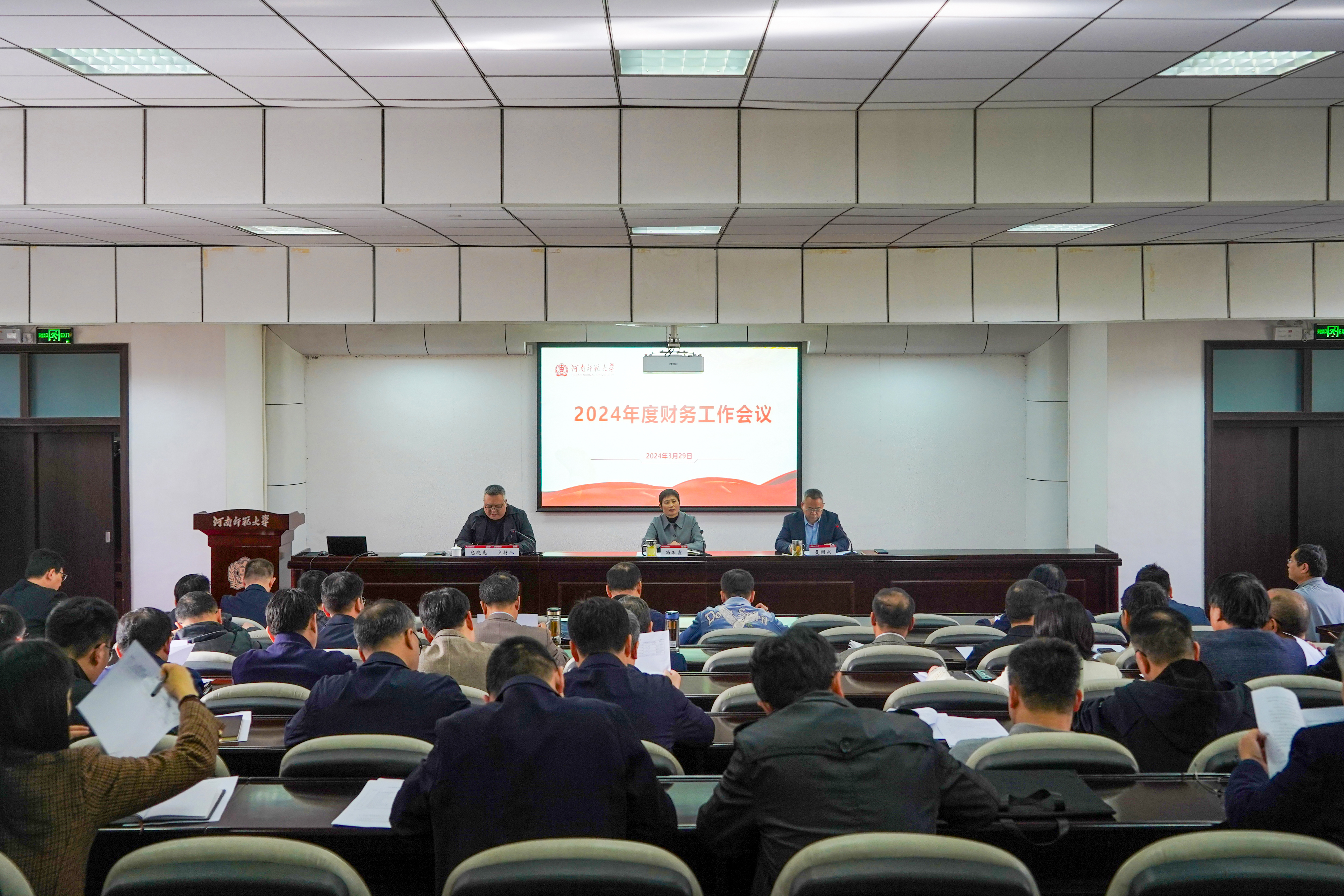